Register
VRUs: An Intersection of Economics and Environmentalism for Upstream Oil and Gas
Insight
•
Updated June 9, 2022
$9 gas is as good a reason as any to lower your methane emissions
Berkleigh Armistead
Darcy Partners
Sustainability
Flaring
Methane Emissions
Introduction
During several recent conversations with operators, the topic of vapor recovery has generated some interesting re-occurring themes; specifically, operators that are currently using vapor recovery units have consistent issues with downtime and extensive maintenance. Some have indicated that they find the units a nuisance to operate (among some other more colorful language). Still, the qualifier echoed by those same operators (at today’s gas prices- see Figure 2) is that “at least they’re making money.” There’s often a premium on VRU gas because of its high BTU content, and operators clearly recognize the economic and environmental impact of installing VRUs on their facilities and minimizing their downtime. On June 21, Darcy will be hosting a sustainability forum featuring Fluidstream, a company that specializes in vapor recovery, and whose product was specifically developed to address the pain points of operators related to vapor recovery units.
The role of vapor recovery to reduce methane emissions and flaring is well established for upstream oil and gas producers. Vapor recovery units are used to capture and compress gas streams, often very low volumes but high BTU content, at crude oil (and sometimes produced water) storage tanks. The recovered gas is then sent to the gas gathering/sales line or other local use such as a fuel gas system. For some operators, especially those with zero routine flaring pledges and gas takeaway infrastructure, VRUs are standard for every new facility and older facilities are often retrofitted to include them. Traditional vapor recovery units typically consist of a compressor, scrubber, variable frequency drive, and a switching device [1] A schematic of an example standard vapor recovery unit is shown in Figure 1; notice that the source is dated to 1968 and the technology has not fundamentally changed a lot since.
Figure 1: VRU Schematic [6]
Economic and Environmental Benefits
Most oil storage tanks are only rated to 1-2 pisg; this means that any gas that finds its way into the tank or comes out of solution from the oil must be vented, sent to flare, or removed via vapor recovery before pressure increases in the tank and causes structural damage. Vented gas, in addition to being a safety hazard on location, contributes to the operator’s overall methane emissions footprint. Environmental factors on their own motivate many operators to install VRUs on their facilities, but as natural gas prices continue to trend upward (Figure 2) from their recent historical lows, VRU installation makes economic sense for a wider range of locations and facilities too. Some Canadian provinces and US states are also looking into (or currently are) bringing additional market-based incentives, (think carbon credits/carbon taxes) for GHG emissions reduction targets.
Figure 2: Henry Hub Natural Gas Price [EIA]
Types of VRU Compressors
The heart and soul of a VRU is the compressor. There are a few different options that can be used for vapor recovery applications these are, broadly speaking: oil flooded rotary screw, rotary vane, reciprocating, vapor jet pump, and some other types that are variations of these basic categories (scroll compressors, eductor style). Each type of compressor has its own ideal operating conditions; for example, oil in flooded rotary screw compressors can be contaminated by rich gas during the compression process, but these types of compressors are the most widely used in VRU service because of their flow rate adaptability.
Figure 3: Rotary Screw Compressor Schematic [5]
Rotary vane compressors are well suited for wet gas and H2S handling but are discharge pressure limited. Reciprocating compressors are not as common, but are still occasionally used for vapor recovery. Vapor recovery units are often sensitive to variable flow rates, temperature, wet gas, sour gas, liquid slugs, and often require frequent maintenance to keep them operating effectively.
Figure 4: Rotary Vane Compressor Schematic [4]
Figure 5: Reciprocating Compressor Schematic [7]
Parting Thoughts
In 2006 the EPA estimated that there were approximately 500,000 oil storage tanks in the United States [6]. This number is still occasionally quoted in publications, but by using our human brains and the estimate of the total number of wells in the US (Figure 6), we can infer that this number has probably increased. The size of the prize, as far as environmental and market incentives are concerned, has never been larger to deploy vapor recovery units, yet the operational complexity of these systems to get them working correctly with minimal downtime may still give some operators a headache. Darcy will be covering vapor recovery in the June 21st Sustainability event where Fluidstream will present how their VRU system addresses many of the previously mentioned limitations of conventional VRU systems- specifically achieving 100% turndown, liquids handling without a scrubber, autonomous controls, and simplistic design with low maintenance (no oil to change, fewer parts).
Figure 6: US Total Wells [EIA]
Sources
[1]https://www.generon.com/what-is-a-vru-how-does-a-vapor-recovery-unit-work/
[2] https://www.msn.com/en-us/money/other/canada-launches-greenhouse-gas-reduction-credits-to-help-tackle-emissions/ar-AAYdl03?ocid=uxbndlbing&fromMaestro=true
[3] https://cimarron.com/frequently-asked-questions-about-vapor-recovery-units-vrus/
[4] https://learnmech.com/wp-content/uploads/2020/05/vane-compressor-diagram.jpg
[5] https://www.researchgate.net/profile/Ahmed-Kovacevic-3/publication/241816817/figure/fig1/AS:315241176027136@1452170761013/Screw-Compressor-Main-Components.png
[6] https://www.epa.gov/sites/default/files/2016-06/documents/llfinalvap.pdf
[7] https://www.theengineerspost.com/types-of-air-compressors/
Related Content
Vehicle-Based Methane Emissions Monitoring - Innovator Comparison
Sustainability
Methane Emissions
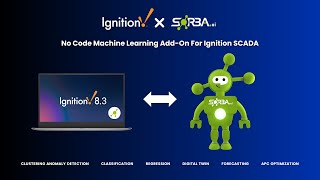
How To Integrate SORBA.ai With Ignition SCADA
Oil & Gas
Sustainability
Completions
Drilling
Flaring
Production
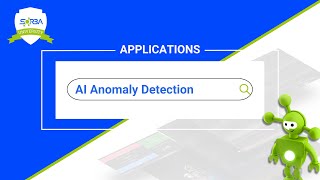
AI Anomaly Detection
Oil & Gas
Sustainability
Completions
Drilling
Flaring
Production
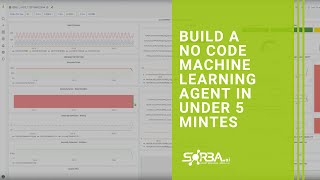
Build a No Code Machine Learning Agent In Under 5 Minutes
Oil & Gas
Sustainability
Completions
Drilling
Flaring
Production